Precast concrete construction is economical
The precast building system saves money, resources and time
Economic factors play an important role for the choice of a suitable building system. This has most notably an effect on housing if large numbers of houses are built. Construction with precast concrete elements offers a great number of advantages in this case.
Fixed final price and completion date for precast buildings
Short construction time compared to traditional building methods
Moreover, you only need a short construction time when building in precast compared to other building methods. In comparison to the in-situ concrete building method, you are up to five times faster. A short construction time means lower costs incurred by the building owner for financing and site facilities.
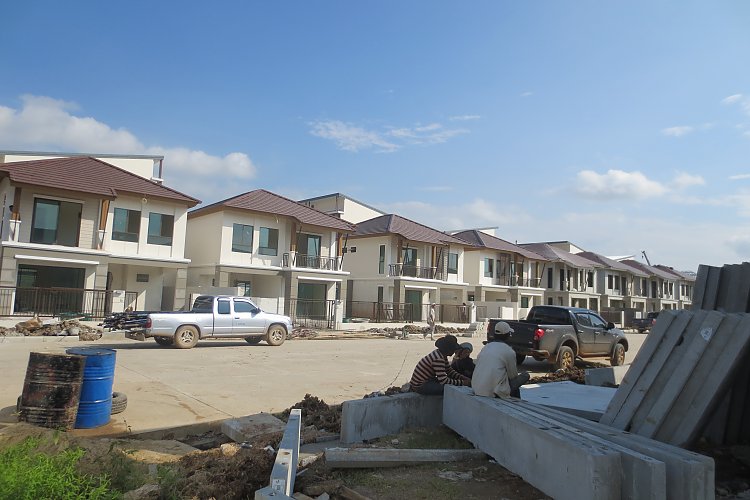
Thailand – economical construction
The Thai company Pruksa builds numerous high-quality houses with identical ground plots and details. The precast concrete elements for the houses are produced in the factory and solely assembled on site, the interior work is carried out and building services are installed. Using the same ground plot for numerous houses, Pruksa is able to reduce their costs because the costs for the design are spread across many houses. The assembly of the elements is also facilitated because the assembly crew always assembles the same elements and details together.Less coordination on site
The industrialized construction with precast concrete requires less monitoring and coordination on site. The precast elements are only assembled on site and the interior work is executed. Therefore, fewer companies are on site and less coordination between these companies is necessary.
Fewer personnel
Since the 1980s, man-hours per square meter have been reduced by more than two thirds as automation has constantly increased since that time. This means that only one third of the workers is needed to produce the same amount of precast concrete elements and labor costs can be reduced significantly.
Both at the production in the plant and at the assembly of the precast concrete elements on site, untrained personnel can be employed.
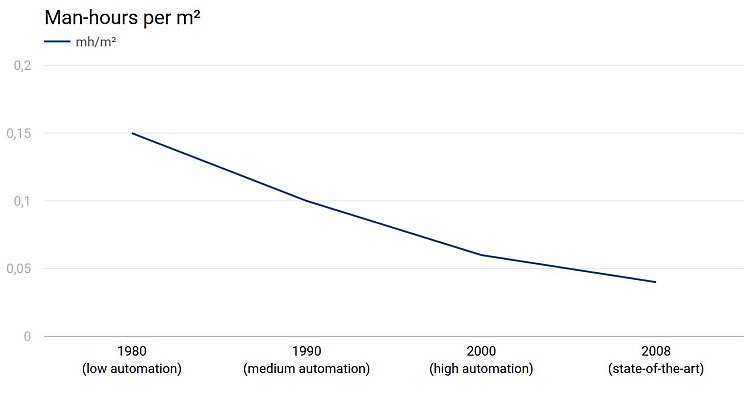
Building material and construction costs savings
Savings in reinforcement and concrete are possible due to the accurate production of precast concrete elements and the utilization of slim building elements. These material savings decrease the production costs of precast concrete elements.
The master computer controls and monitors the production facility. Therefore, material like concrete, construction steel, etc. can be used in a resource-saving way and optimally employed. The concrete compound is adjusted accurately and mixed in the batching plant of the factory.
Reduced maintenance costs for precast concrete buildings
Precast concrete buildings do not need any maintenance for a period of at least 50 years because the material is sturdy and durable. This reduces maintenance costs significantly.
Lower construction costs
The concrete panel construction consists of load-bearing walls and floors and substitutes frame and skeleton structures. No additional bracing system is necessary and construction costs decrease.
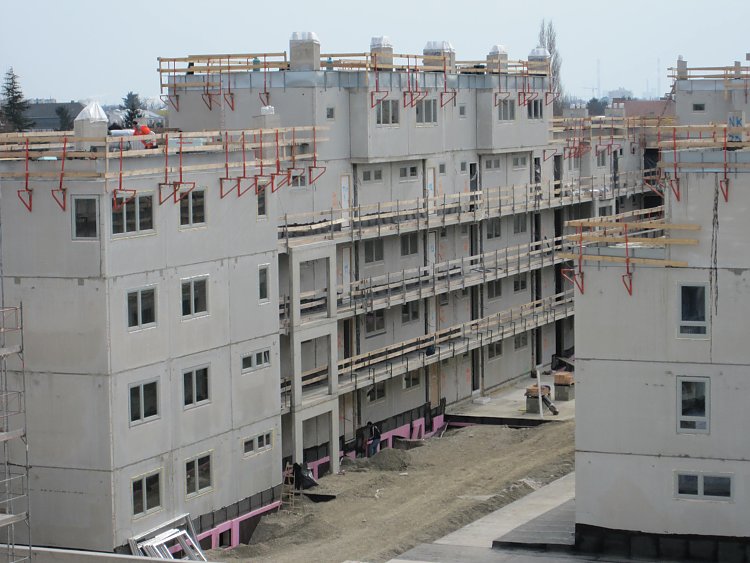